Как роботизировать склад: от анализа бизнес-процессов и расчета экономической эффективности до выбора роботов
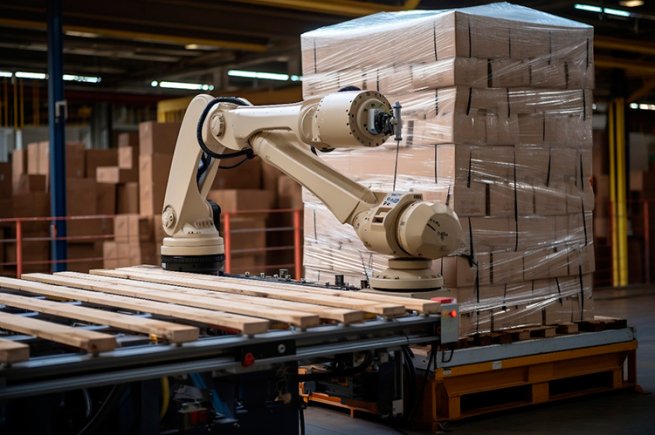
время публикации: 10:00 15 июля 2025 года
@Freepik (AI-generated)
На деле именно так сегодня выглядит грамотная роботизация. Она начинается с рентгена всех товарных потоков, опирается на холодную экономику TCO и заканчивается гибридной архитектурой, где AMR, сортировочные шлюзы и люди работают как единый организм.
В колонке Екатерина Родина, директор по внешнему развитию ГК «Автомакон» разбирается, почему карта процессов экономит треть бюджета, как не зарыть ROI в скрытых издержках, и чем один хорошо спроектированный пилот ценнее сотни презентаций поставщиков.
Первый шаг – детальное картирование текущих процессов склада. Надо схематизировать всю цепочку от приемки товара до отгрузки, зафиксировать места хранения, сортировки и комплектования, а также указать участников и используемые носители.
Такой аудит as-is обнаружит пропущенные или неправильно работающие процессы и выявит узкие места, мешающие эффективности. Уже на этапе моделирования становится понятно, какие операции тянутся в конец цепочки, где часто возникают простои и ошибки, и какие рутинные задачи стоит автоматизировать в первую очередь. Это и есть быстрые победы – высокочастотные или тяжелые работы, которые легко положить на робота или конвейер и сразу получить ощутимый эффект.
Грамотная разработка карты процессов позволяет заранее учесть все технические интерфейсы и роли сотрудников, что экономит ресурсы проекта и снижает число сюрпризов при интеграции.
По оценкам Giftery, автоматизация целевых операций позволяет сократить операционные затраты до трети бюджета проекта. А комплексное планирование с учетом процессов и сценариев «что-если» уменьшает риск технических ошибок. На крупных проектах для этого проводят специальные тесты и логирование интеграционных событий, чтобы вовремя обнаружить и исправить проблемы до запуска в работе.
После описания процессов важно оценить эффективность внедрения. Учтите все статьи расходов. Помимо покупки роботов потребуется интеграция с существующими системами, обучение персонала, изменение инфраструктуры и техобслуживание. Если эти скрытые статьи не включить в расчет, срок окупаемости проекта резко возрастает.
Например, на этапе внедрения AMR-роботов нужно предусмотреть время на наладку, развертывание, обучение сотрудников и возможную перебазировку хранилища. Эти скрытые затраты зачастую упускают из виду, а зря – именно они могут отложить возврат инвестиций на годы.
Помимо общих затрат важно измерять ключевые показатели работы склада. Широко применяемый в промышленности индекс OEE позволяет отслеживать простои, сниженную скорость и брак в работе оборудования. В логистике его можно адаптировать для отслеживания эффективности роботизированных линий или ВЭСов. Также учитываются энергозатраты на работу подвижного состава, расходы на обслуживание и поддержку и стоимость простоев. Только полный учет TCO (Total Cost of Ownership), с учетом стоимости роботов и операционных расходов, дает верную картину рентабельности.
По оценке Ассоциации интеграторов, срок окупаемости может варьироваться от 2,5 до 6 лет, в зависимости от направления работы. К примеру, Wildberries отмечает, что вертикальный сортировочный конвейер полностью окупился за полгода благодаря большим объемам отгрузки. При этом важно строить несколько сценариев окупаемости, учитывая консервативную оценку трудосбережений. Иначе есть риск недооценить влияние эксплуатационных расходов, например, простоев из-за форс-мажоров или длительного обучения персонала.
Технология выбирается с учетом типа товара, объемов операций и требуемой скорости. Так, AMR-роботы отлично подходят для динамичных складов с большим потоком паллет и ящиков, они гибкие в переналадке маршрутов и масштабируемы при росте нагрузки. Но они не годятся для нестандартного груза или хаотично стоящих на полу коробок. Тут может потребоваться конвейерная или башенная система (AS/RS).
Также учитывают разные классы роботов: промышленные манипуляторы для переброски мелкой штучной продукции, AGV и AMR для транспортировки поддонов и стеллажей, и сортировочные шлюзы типа Cross-Belt или Tilt-Tray для посылок и мелких коробок.
Оптимальное решение часто оказывается смешанным. Конвейер + AMR + WES-софт – мощная комбинация. Конвейер быстро обрабатывает непрерывный поток, AMR доставляют паллеты к зонам отбора, а WES-алгоритмы координируют весь процесс. Например, эксперты отмечают, что совместное применение AS/RS, конвейеров и мобильных роботов позволяет хранить товары более плотно, ускорить комплектацию и заметно снизить количество ошибок. При этом интеграция с WMS-системой дает быстрый доступ к данным о позициях товаров и упрощает масштабирование.
Российские компании демонстрируют разные примеры. Например, компания Wildberries внедрила робота-стеллажника по системе товар к человеку, роботизированные вилочные погрузчики для перемещения паллет и промышленные роботы с машинным зрением для перекладки товаров между конвейерами. Компания отмечает, что гибридная схема роботизации, около 50% процессов, оказалась эффективнее попытки полной автоматизации.
Также показателен пример сети « Магнит». В новом распределительном центре под Подольском ритейлер задействовал роборуки для укладки коробов на паллеты, конвейеры для основного потока, а также протестировал автономных мобильных роботов и роботизированных погрузчиков для перемещения грузов между зонами.
Читайте также: Роботизация складов и Big Data — как устроена автоматизация бизнес-процессов на базе глубоких данных?
Перед полномасштабным развертыванием рекомендуется пилотировать новую систему на реальной площадке и при этом не останавливать весь склад. Для этого обычно выделяют ограниченную зону или часы с меньшей загрузкой. При этом на пилоте собирают детальные данные об эффективности: время подъема, задержки, энергопотребление и т.д.
По результатам пилота вносятся коррективы в ТЗ – иногда это мелочи вроде добавления датчиков и настройки ПО. Так, в одном проекте после тестовой эксплуатации роботов выяснилось, что им требуются дополнительные ультразвуковые метки и уточненная логика управления – это исправили до этапа масштабного запуска.
Одновременно с техническим тестированием важно готовить персонал. Ключевые сотрудники должны пройти обучение заранее. Они должны разбираться в интерфейсах управления, базово уметь перезапускать систему, понимать принципы безопасности. Параллельно нужно налаживать сервисную поддержку – нередко интегратор обеспечивает 24/7-доступ к специалистам и быстрому ремонту. В финале проекта рекомендуется выводить систему частями, параллельно работая с прежними методами, чтобы исключить длительные простои.
Переход от пилота к полной роботизации требует четкой координации. Нужно достичь уверенной работы системы в тестовом режиме, обучить людей и обеспечить поддержку. Тогда склад плавно превратится в гибридное хранилище, где люди и роботы выполняют свои задачи без сбоев и простоев.
С чего начать роботизацию склада? Где кроются «финансовые ловушки» и как их избежать в таких проектах? Рекомендации по управлению рисками внедрения от эксперта.
Представьте склад, где роботы не просто катаются между стеллажами, а сами умеют подстраивать маршруты под пробки на конвейере и возвращают вложенные в них миллионы быстрее, чем окупается классический погрузчик. Звучит как фантастика? 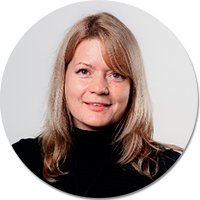
В колонке Екатерина Родина, директор по внешнему развитию ГК «Автомакон» разбирается, почему карта процессов экономит треть бюджета, как не зарыть ROI в скрытых издержках, и чем один хорошо спроектированный пилот ценнее сотни презентаций поставщиков.
С чего начать роботизацию
Первый шаг – детальное картирование текущих процессов склада. Надо схематизировать всю цепочку от приемки товара до отгрузки, зафиксировать места хранения, сортировки и комплектования, а также указать участников и используемые носители.
Такой аудит as-is обнаружит пропущенные или неправильно работающие процессы и выявит узкие места, мешающие эффективности. Уже на этапе моделирования становится понятно, какие операции тянутся в конец цепочки, где часто возникают простои и ошибки, и какие рутинные задачи стоит автоматизировать в первую очередь. Это и есть быстрые победы – высокочастотные или тяжелые работы, которые легко положить на робота или конвейер и сразу получить ощутимый эффект.
Грамотная разработка карты процессов позволяет заранее учесть все технические интерфейсы и роли сотрудников, что экономит ресурсы проекта и снижает число сюрпризов при интеграции.
По оценкам Giftery, автоматизация целевых операций позволяет сократить операционные затраты до трети бюджета проекта. А комплексное планирование с учетом процессов и сценариев «что-если» уменьшает риск технических ошибок. На крупных проектах для этого проводят специальные тесты и логирование интеграционных событий, чтобы вовремя обнаружить и исправить проблемы до запуска в работе.
Когда роботы окупятся и как избежать финансовых ловушек
После описания процессов важно оценить эффективность внедрения. Учтите все статьи расходов. Помимо покупки роботов потребуется интеграция с существующими системами, обучение персонала, изменение инфраструктуры и техобслуживание. Если эти скрытые статьи не включить в расчет, срок окупаемости проекта резко возрастает.
Например, на этапе внедрения AMR-роботов нужно предусмотреть время на наладку, развертывание, обучение сотрудников и возможную перебазировку хранилища. Эти скрытые затраты зачастую упускают из виду, а зря – именно они могут отложить возврат инвестиций на годы.
Помимо общих затрат важно измерять ключевые показатели работы склада. Широко применяемый в промышленности индекс OEE позволяет отслеживать простои, сниженную скорость и брак в работе оборудования. В логистике его можно адаптировать для отслеживания эффективности роботизированных линий или ВЭСов. Также учитываются энергозатраты на работу подвижного состава, расходы на обслуживание и поддержку и стоимость простоев. Только полный учет TCO (Total Cost of Ownership), с учетом стоимости роботов и операционных расходов, дает верную картину рентабельности.
По оценке Ассоциации интеграторов, срок окупаемости может варьироваться от 2,5 до 6 лет, в зависимости от направления работы. К примеру, Wildberries отмечает, что вертикальный сортировочный конвейер полностью окупился за полгода благодаря большим объемам отгрузки. При этом важно строить несколько сценариев окупаемости, учитывая консервативную оценку трудосбережений. Иначе есть риск недооценить влияние эксплуатационных расходов, например, простоев из-за форс-мажоров или длительного обучения персонала.
Выбор технологической архитектуры
Технология выбирается с учетом типа товара, объемов операций и требуемой скорости. Так, AMR-роботы отлично подходят для динамичных складов с большим потоком паллет и ящиков, они гибкие в переналадке маршрутов и масштабируемы при росте нагрузки. Но они не годятся для нестандартного груза или хаотично стоящих на полу коробок. Тут может потребоваться конвейерная или башенная система (AS/RS).
Также учитывают разные классы роботов: промышленные манипуляторы для переброски мелкой штучной продукции, AGV и AMR для транспортировки поддонов и стеллажей, и сортировочные шлюзы типа Cross-Belt или Tilt-Tray для посылок и мелких коробок.
Оптимальное решение часто оказывается смешанным. Конвейер + AMR + WES-софт – мощная комбинация. Конвейер быстро обрабатывает непрерывный поток, AMR доставляют паллеты к зонам отбора, а WES-алгоритмы координируют весь процесс. Например, эксперты отмечают, что совместное применение AS/RS, конвейеров и мобильных роботов позволяет хранить товары более плотно, ускорить комплектацию и заметно снизить количество ошибок. При этом интеграция с WMS-системой дает быстрый доступ к данным о позициях товаров и упрощает масштабирование.
Российские компании демонстрируют разные примеры. Например, компания Wildberries внедрила робота-стеллажника по системе товар к человеку, роботизированные вилочные погрузчики для перемещения паллет и промышленные роботы с машинным зрением для перекладки товаров между конвейерами. Компания отмечает, что гибридная схема роботизации, около 50% процессов, оказалась эффективнее попытки полной автоматизации.
Также показателен пример сети « Магнит». В новом распределительном центре под Подольском ритейлер задействовал роборуки для укладки коробов на паллеты, конвейеры для основного потока, а также протестировал автономных мобильных роботов и роботизированных погрузчиков для перемещения грузов между зонами.
Читайте также: Роботизация складов и Big Data — как устроена автоматизация бизнес-процессов на базе глубоких данных?
Управляем рисками внедрения
Перед полномасштабным развертыванием рекомендуется пилотировать новую систему на реальной площадке и при этом не останавливать весь склад. Для этого обычно выделяют ограниченную зону или часы с меньшей загрузкой. При этом на пилоте собирают детальные данные об эффективности: время подъема, задержки, энергопотребление и т.д.
По результатам пилота вносятся коррективы в ТЗ – иногда это мелочи вроде добавления датчиков и настройки ПО. Так, в одном проекте после тестовой эксплуатации роботов выяснилось, что им требуются дополнительные ультразвуковые метки и уточненная логика управления – это исправили до этапа масштабного запуска.
Одновременно с техническим тестированием важно готовить персонал. Ключевые сотрудники должны пройти обучение заранее. Они должны разбираться в интерфейсах управления, базово уметь перезапускать систему, понимать принципы безопасности. Параллельно нужно налаживать сервисную поддержку – нередко интегратор обеспечивает 24/7-доступ к специалистам и быстрому ремонту. В финале проекта рекомендуется выводить систему частями, параллельно работая с прежними методами, чтобы исключить длительные простои.
Переход от пилота к полной роботизации требует четкой координации. Нужно достичь уверенной работы системы в тестовом режиме, обучить людей и обеспечить поддержку. Тогда склад плавно превратится в гибридное хранилище, где люди и роботы выполняют свои задачи без сбоев и простоев.
Екатерина Родина,
директор по внешнему развитию ГК «Автомакон».
Для NEW RETAIL
0
Последние новости
Самое популярное
-
Маркетплейсы больше не в тренде: продавцы уходят в интернет-магазины
-
Как переводить деньги из-за границы в Россию в 2025 году: все способы с плюсами ...
-
Жизнь после сделки: как перестраиваются FMCG-бренды под новых собственников
-
Топ-очередь: выделяем приоритетные запросы для чат-бота
-
Рынок БАДов: как цифровая маркировка изменила правила игры